Manual Handling Training Courses By Industry Experts
Custom manual handling training onsite at your workplace, job site, office or online.
Manual handling training for construction, warehouse, freight, logistics, manufacturing, university, government departments and more.
Our highly skilled instructors draw on their knowledge of dynamic movement, experience of clinical assessment and real life examples of workplace injuries.
Cost effective, engaging manual handling training that delivers measurable results to achieve your objectives.
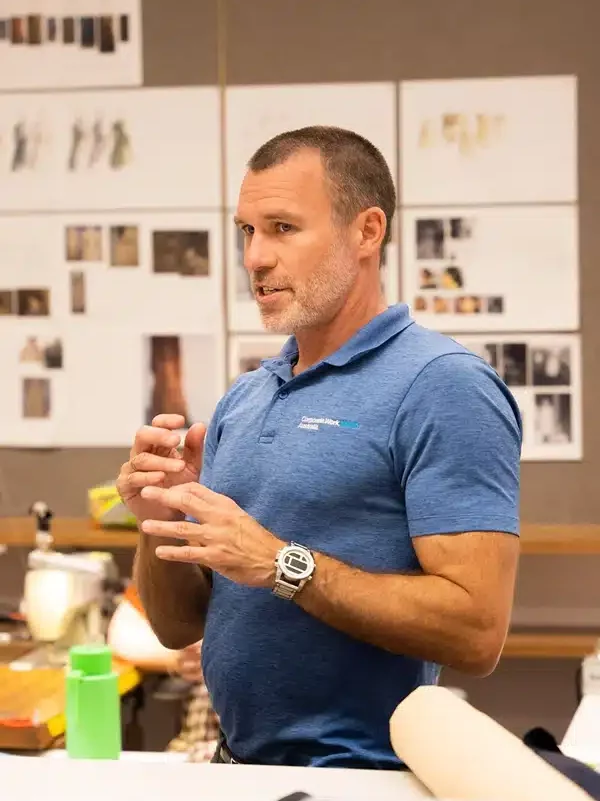
Face To Face Manual Handing Courses
Manual handling training for the office worker or those who perform occasional manual handling tasks
Learn more about this course
Learning outcomes:
- Define manual handling and common workplace manual handling tasks completed within the workplace
- Review research findings surrounding manual handling training, including what training should include
- Review common manual handling technique strategies
- Discuss workers duties, including participation and consultation with regards to manual handling
- Define manual tasks risk factors – what is a hazardous manual task?
- Educate workers on simple risk assessment strategies including the hierarchy of control
- Complete practical training on key manual handling tasks within the workplace, and use of any mechanical assistance if required
- Answer any further questions related to manual tasks in the workplace
Customised Office Manual Handling Training inclusions:
- 1.5 hour training session
- Up to 20 team members per session
- 45-60min theory/classroom training + 30-45min practical training
- Training sessions are delivered by registered health professionals
- Includes virtual or face to face site view, customization of course creation/content, and delivery of training
- Records and documentation. We will provide you with a PDF of the training materials delivered, certificate of attendance and feedback forms collected from participants
Generic Office Manual Handling Training inclusions:
- 1.5 hour training session
- Up to 20 team members per session
- 45-60min theory/classroom training + 30-45min practical training
- Training sessions are delivered by registered health professionals
- Generic office manual handling training presentation (non customised photos and videos of tasks)
- Records and documentation. We will provide you with a PDF of the training materials delivered, certificate of attendance and feedback forms collected from participants
Course location:
Our CWHA trainers will attend your workplace and conduct training onsite at your company so that attendees can be trained in their work environment and training can be tailored to specifically suit your company.
Investment:
Starting at $600+GST for generic office manual handling training and $950+GST for customised office manual handling training | Follow up training sessions $480 + GST. Please call 1300 951 519 or email admin@corporateworkhealth.com for a quote.
Looking for something different?
This course can have content or training time adjusted to suit your needs. Just let us know what you are looking for!
Manual handling training for those who perform frequent or heavy manual handling tasks
Find out more about this course
Learning outcomes:
- Define manual handling and common workplace manual handling tasks completed within the workplace
- Review research findings surrounding manual handling training, including what training should include
- Review common manual handling technique strategies
- Educate workers on the semi-squat and leg lift techniques
- Educate workers on twisting and turning, pushing and pulling and team lifting
- Discuss workers duties, including participation and consultation with regards to manual handling
- Define manual tasks risk factors
- Educate workers on simple risk assessment strategies including the hierarchy of control
- Workshop common / high risk manual handling tasks and undertake apply risk factors and possible control measures basic
- Step by step practice of key high risk tasks with consultation on any risk reduction improvements discussed
- Use of trolleys, cranes or lifters if appropriate
- Answer any further questions related to manual tasks in the workplace
Course details / inclusions:
- 2 – 3 hour training session/s according to your organisational and work group needs
- Up to 15 team members per session
- 75-90min theory/classroom training + 60-75min practical training
- Training sessions are delivered by registered health professionals
- Suited to those workers who perform frequent/heavy manual handling tasks within their job role i.e. warehouse, logistics, retail, construction, manufacturing
- Includes pre-training virtual meeting, customization of course creation/content, and delivery of training
What’s involved in designing your training:
Our customised manual handling training involves a 4 step process:
- Face to face or virtual consultation and site visit consultation with key stakeholders to discuss current manual handling practices. Please note: CWHA will take photos and videos of manual tasks performed for learning and teaching purposes.
- Manual handling training program design – CWHA will then create a customised manual handling package specific to your workplace tasks, hazards, risk assessment tools and control measures.
- Manual handling training sessions 2 – 3 hours onsite within your workplace.
- Records and documentation. We will provide you with a PDF of the training materials delivered, certificate of attendance and feedback forms collected from participants.
Course location:
Our CWHA trainers will attend your workplace and conduct training onsite at your company so that attendees can be trained in their work environment and training can be tailored to specifically suit your company.
Investment:
Starting at $900+GST per session & $350 – $500 + GST site visit and design. Please call 1300 951 519 or email admin@corporateworkhealth.com for a quote
Additional service offerings:
For an additional fee a report can be prepared which highlights the hazards / challenges raised by team members during the session, as well as possible control measures which can be consulted over further to address the hazards/challenges. Please let us know if you would like included in your quote. Additional estimated cost $250+GST.
Looking for something different?
This course can have content or training time adjusted to suit your needs. Just let us know what you are looking for!
Combined manual handling & office workstation training for the office worker
See what is involved in this course
Learning outcomes:
- Define manual handling and common workplace manual handling tasks completed within the workplace
- Review common manual handling technique strategies
- Discuss workers duties, including participation and consultation with regards to manual handling
- Educate workers on manual tasks risk factors and the hierarchy of control
- Complete practical training on key manual handling tasks within the workplace, and use of any mechanical assistance if required
- Educate workers on best practice workstation set up (chair, desk, computer accessories)
- Educate workers on seated postures and how to minimise musculoskeletal strains and sprains in the office workplace
- Answer any further questions related to manual tasks or ergonomics in the workplace
Course details / inclusions:
- 2 hour training session
- Up to 20 team members per session
- 60-75min theory/classroom training + 45-60min practical training
- Training sessions are delivered by registered health professionals
- Includes pre-training virtual meeting, customization of course creation/content, and delivery of training
- Records and documentation. We will provide you with a PDF of the training materials delivered, certificate of attendance and feedback forms collected from participants
Course location:
Our CWHA trainers will attend your workplace and conduct training onsite at your company so that attendees can be trained in their work environment and training can be tailored to specifically suit your company.
Investment:
Starting at $750+GST for course design and training session | Follow up training sessions $600 + GST. Please call 1300 951 519 or email admin@corporateworkhealth.com for a quote.
Looking for something different?
This course can have content or training time adjusted to suit your needs. Just let us know what you are looking for!
Book An Online Meeting With One Of Our Directors
Our directors have over 20 years experience! A online video call is recommended for organisations wanting manual handling training or risk assessments. Choose the state you require service delivery in via the buttons below to book a FREE online meeting or call and we will find a time that suits you.
Organisations Who Trust Our Manual Handling Training
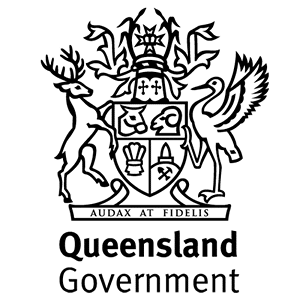
government
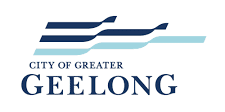
council
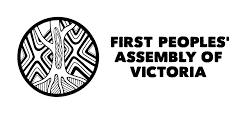
nonprofit
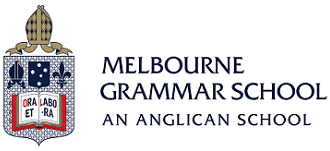
education
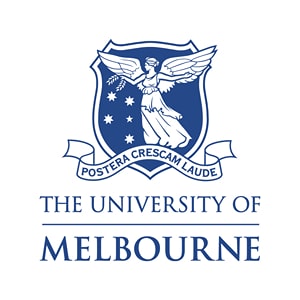
university
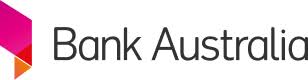
banking
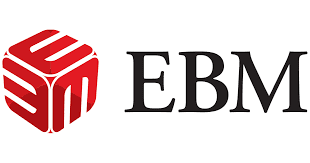
finance
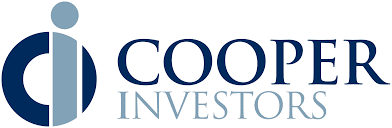
insurance

superannuation
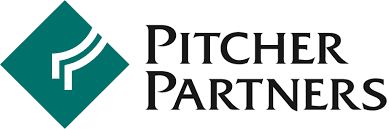
accounting
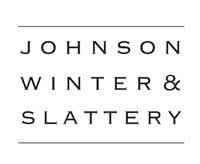
legal
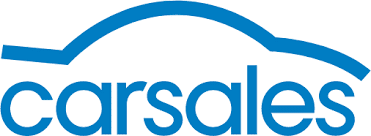
technology
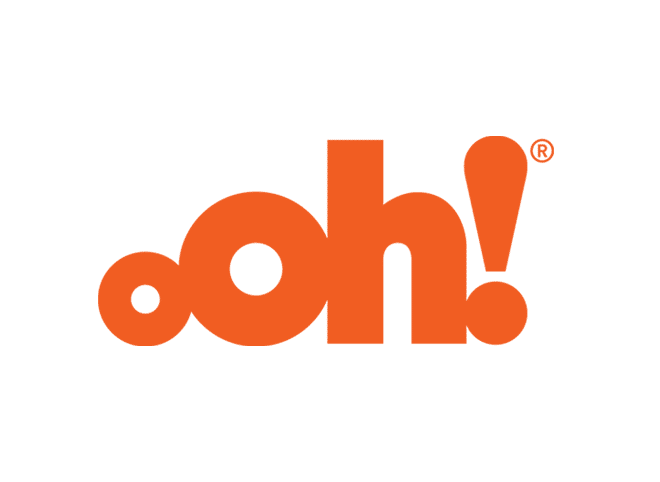
communication
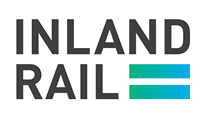
transport
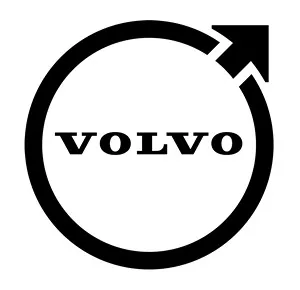
logistics
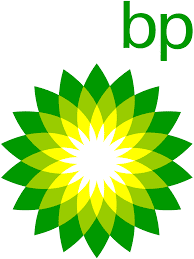
mining
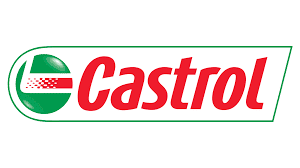
resources

manufacturing
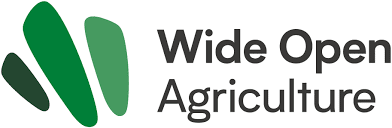
agriculture
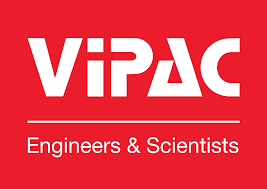
engineering
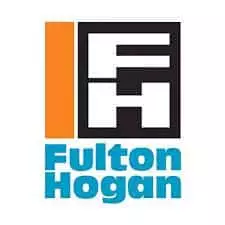
construction
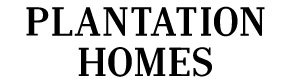
property
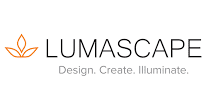
architecture
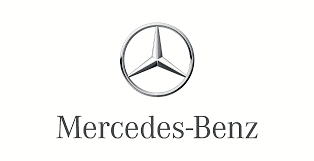
retail
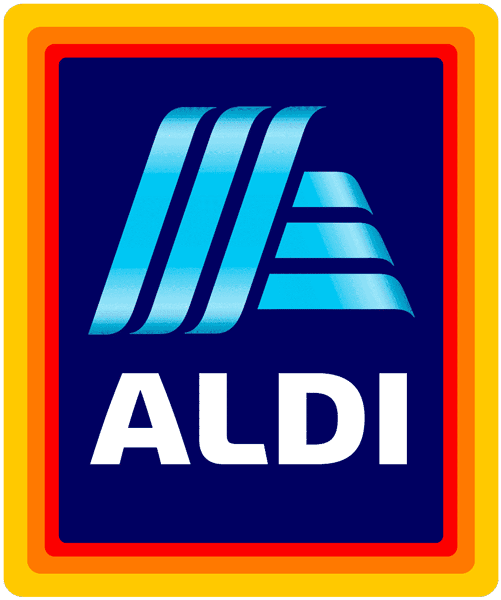
supermarket
Onsite Manual Handling Case Study
A large government council organisation identified the need to review manual handling hazards and risks and implement manual handling training across multiple work sites and with various work departments and teams that consisted of approximately 250 workers.
Manual handling accounted for the majority of work related strains and sprains across the departments parks and gardens, waste management and roads. Cumulative injuries combined with an ageing workforce were also identified as challenges for the workplace.
Background & Reason For Consultation
- Manual handling hazard and risk training had not been conducted within the organisation for several years.
- Manual handling injuries accounted for the majority of workplace strains and sprains across all departments.
- Cumulative injuries and an ageing workforce were also identified as challenges for the business.
Proposed Services & Implementation
Phase 1: Consultation with key stakeholders to discuss manual handling hazards and risks, injury history and specific training needs.
Phase 2: Consultation with workers in each department across the different work sites to identify primary manual handling hazards and risks relating to their specific job role.
Phase 3: Development of a customised manual handling program that focused on a 2 stage delivery.
Stage 1 – Generic 1 hour manual handling hazard and risk management training
Stage 2 – 1 hour onsite task specific training delivered to workers at their specific work site and job roles
Phase 4: Reporting and consultation with key stakeholders regarding manual handling hazards and risk identified and consideration of control measures according to the risk control hierarchy.
Hazards and Risks Identified
- Manual handling hazards and risks identified according to specific department and job role specific tasks.
Outcomes & Recommendations
Outcomes
- Primary manual handling hazards and risks identified within specific departments and job roles.
- Control measure recommendations provided for problematic manual handling hazards and risks.
- 90% of workers across all departments and teams participated and completed the 2 stage manual handling hazard and risk training.
Further Recommendations
- Follow up consultation with key workers within each department and work groups to ensure workers continue to embrace and implement a risk management approach to working.
- Develop focused working groups and undertake detailed manual task risk management for specific manual handling hazards identified.
- Implement refresher training on an annual basis as well as targeted specific education sessions within tool box talks.
Custom Manual Handling Training For Job Site, Office or Workplace
Our manual handling courses can be customised for your employees to enjoy a safe work environment and live a healthy life for the long term – rather than being just another standard health and safety course. By delivering a worksite manual handling training course tailored to your workplace we create solutions that really work by making a difference to your workers health and safety, and improving your profitability at the same time.
Corporate Work Health Australia is proud to rise above the rest. We ensure that our training courses meet our client’s exact training needs including visual, practical and written materials where appropriate.
Different industries require different training. This is why we work collaboratively with our clients to customise our programs so they deliver task specific training that addresses the manual handling challenges faced in their particular business. We have extensive experience in manual handling training for freight and logistics, warehouse and manufacturing, construction, office workers or government departments, universities and more.
Read More
Manual Handling Courses Designed For Long Term Health & Safety
Manual handling injuries are the product of poor work practices and a lack of effective ergonomic systems. A culture that ignores an employee’s complaints about the twinges in their back when they complete certain tasks fails to notice the early warning signs of a problem that could develop into something much greater.
Companies with a culture of open communication take such complaints as a red flag that needs to be addressed. A simple tweak to the workspace or a new chair could make all the difference, or it could be through training that the team learns how best to handle materials in a manner that protects their bodies, which can be accomplished through job site manual handling training.
Manual Handling Training Delivered by Qualified Health Professionals
When you opt for a manual handling program from the team here at Corporate Work Health Australia, you gain the knowledge, expertise and advice from professionals with practical experience. What’s more, our manual handling courses are carried out by qualified physiotherapists, exercise physiologists, occupational therapists and osteopaths.
We believe that every business has the potential to embrace a better way of working that can lead to even greater profits. Better still, morale will receive a welcome boost when you engage the best manual handling training available in Australia today.
Limit Risk In Your Workplace With Custom Manual Handling Training
Those that participate in the manual handling training course gain a greater understanding of the risks that are present in the workplace and how to instruct their staff in terms of manual handling. The education gained will afford you the chance to streamline and improve your processes and practices, even in small ways, which can lead to the greater overall wellbeing of those you employ.
Training Can Reduce Injuries And Compensation
Manual handling is the most common cause of injury in Australia. 107,355 serious claims were lodged in the 2014-15 financial year. Injury and musculoskeletal disorders led to 90% of these serious claims, with the most common traumatic joint/ligament and muscle/tendon injuries (almost 45%). In 2012–13, work-related injury and disease cost the Australian economy $61.8 billion. Injuries accounted for $28 billion (45%) of the cost.
Manual handling (now manual tasks 2010) means more than just lifting or carrying something. The term ‘manual tasks’ is used to describe a range of activities including lifting, lowering, pushing, pulling, carrying, moving, holding or restraining an object, animal or person. This means that all of your workers are exposed to and are at risk of manual handling injuries. Australian WHS (OH&S) legislation requires employers to identify, assess and control workplace hazards.
One of these hazards is the risk of injury caused by manual tasks. The national standard for manual tasks requires that all tasks in your workplace which involve manual handling are identified and that the risk of injury is assessed. Where there is risk of injury, suitable ‘control measures’ must be introduced. Manual handling training is one such control measure.
View more workplace injury statistics to see why manual handling training and courses are essential visit the safe work australia website.
Excellence in Manual Tasks Training
All our manual handling training courses are written using evidence-based material and the most up to date Australian legislation. Corporate Work Health Australia’s training team are fully qualified Physiotherapists, Osteopaths or Exercise Physiologists who pride themselves on delivering effective, easy to understand, jargon free training, best suited for up to 12 workers. Corporate Work Health Australia brings a wealth of experience of working across a broad spectrum of both public and private sectors of industry offering a full and varied portfolio of services aimed at reducing the costs associated with musculoskeletal injury.
Easy to Understand Materials Handling Courses
Our fully qualified training team can provide ‘real life’ examples of injuries they treat daily which reinforces the importance of applying good techniques and teaching the ‘why’ behind the ‘how’ of good technique that people can relate to. The training ensures delegates acquire safe lifting and materials handling skills that are specific to their work environment and reinforce the importance of good technique being applied to all aspects of everyday life. The training also has a strong focus on involving workers in the risk management processes.
A worksite manual handling course always contains a lot of information that at first glance seems obvious, but in truth, has never really been vocalised within the workplace to that point. Sometimes for a company to change its ways an impartial outside voice is needed to discuss such issues and pinpoint the possible negative outcomes that could arise from a failure to change.
Specialised Manual Handling Training Courses
At Corporate Work Health Australia, we specialise in tailoring our manual handling training methods to the companies that we work for. Over an hour and a half, or two and a half hours, your team can engage with practical and theoretical components that are relevant to their work. Instead of choosing an off the shelf program that delivers generic information, choosing to directly engage the workforce enables practical education and allows your team to practice manual handling tasks in the workplace.
Any business that believes that they could do things differently to reduce the number of injuries reported as a result of poor practices should first speak with their workers to determine where they see problems. Systems are often designed in isolation from practical application and it is only when feedback is sought that any problematic elements come to light.
For your manual handling program *, your workshop could also involve a session that partly focuses on office ergonomics and manual handling theory and practical. By the end of the session, your workers will have been trained in the best way to complete their job. Contact us to discover which is the right package for your business.
Process
1. Enquiry
Call, email or complete a form. Let us know what you want to achieve or the problems you are having.
2. Consultation
Phone, video call or face to face. We will discuss your needs, make some suggestions and provide a quote.
3. Assessment
Your assessment and/or training package is 100% tailor made to suit your needs, budget and service requirements.
4. Training
Onsite, online or both. Your personalised package is delivered by health professionals with extensive clinical and teaching experience.
5. Results
We have helped thousands of people at some of Australia’s top companies. Our team will work with you every step of the way to ensure you achieve the right results for your company and for your workers.
Manual Handling Training Benefits For Companies
- Control and minimise the costs of workplace injuries from manual tasks.
- Reductions in back injuries, shoulder injuries and repetitive injuries.
- Comply with workplace health and safety legislation to provide a safe workplace.
- Improve worker’s understanding of the risk assessment and risk control processes.
- Increase the participative approach to reducing manual tasks risk factors and workplace safety culture.
- Decreased absenteeism & increased productivity.
Manual Handling Training Benefits For Employees
- Enhanced skills in identifying manual handling hazards and risks in the workplace
- Enhanced skills in manual handling risk management in the workplace
- Enhanced skills in understanding risk management and applying the risk control hierarchy to solving manual handling hazards in the workplace
- Improved manual tasks skills i.e. general and work specific tasks
- Reduced exposure to health and safety risk
Free Basic Manual Handling Risk Evaluation
Answer a few questions and receive a free online consultation with one of our highly experienced occupational health professionals
Frequently Asked Questions
What Are The Benefits of Onsite Manual Handling Assessments for Employees
When it comes to health and safety, the PCBU (person, company or business undertaking), also known as the employer, has a duty of care to provide a safe workplace, ensure they have appropriate risk management strategies in place and provide the appropriate PPE and training to employees/workers.
Workplaces where workers undertake manual handling as part of their job role should be undertaking manual tasks hazard identification, manual handling risk assessments and provide risk management and manual handling training as part of their overall OHS risk management process.
Workers who undertake manual handling on a daily basis are likely to benefit from manual handling training on a regular basis (6 monthly or annual basis), whereas workers who infrequently handle loads i.e. office workers may only need training every 2 years as their risk exposure is less.
Do employees have responsibilities?
When it comes to manual handling in the workplace, employees have the following responsibilities:
- Follow all reasonable instructions in relation to manual handling procedures
- Engage in the consultative process
- Report manual handling hazards to their immediate supervisor/branch manager; and
- Undertake and apply manual handling training as required
Can I implement a “No Lifting Policy”?
A workplace can implement their own policies and procedures with regards to manual handling, however it is important that the business/employer understands the practicality of doing so. In many workplaces it is simply not feasible or practical to implement a no lifting policy as there is likely to be some type of manual task to be conducted in a workplace. Therefore creating a policy that workers/employees cannot adhere to is not appropriate.
In many circumstances a business may look to implement a no lifting policy with regards to a specific task or item. Mechanical aids may be more appropriate to move the load and the hazard/risk associated with manually moving these loads may be too great. A business is likely to ensure they have a safe work method statement relating to how this task should be performed.
What constitutes a Manual Handling operation?
Manual handling is defined as:
Any activity that requires someone to exert a force in order to:
- Grasp
- Manipulate
- Strike
- Throw
- Carry
- Move (lift, lower, push, pull)
- Hold or restrain an object or body part
Workers who perform these tasks are at risk of manual handling injuries. Workers should be educated on manual handling risk management and best practices relating to manual handling. Contact us at Corporate Work Health Australia
What are the recommended weight limits for lifting?
Neither the regulations or codes of practice specify weight limits for lifting.
This is because there are many factors that impact on the risk, not just the weight of the item being handled.
Some workplaces will implement weight limits for single or dual person lifting as well as weight limits according to height ranges. They have likely implemented these internal company policies and procedures as part of their manual tasks risk management process.
What does a manual handling training course include?
Manual handling training course design and delivery should involve the following processes to ensure a customised course that is applicable to your workplace
Step 1. Consultation with workers regarding work tasks performed, hazardous manual handling tasks, review of manual handling injury statistics and mechanisms.
Step 2. Site visit and viewing of manual tasks performed. In some circumstances this is not possible and therefore providing photos and videos and other documents relating to policies and procedures and manual handling training materials will suffice
Step 3. Training course design
Step 4. Training delivery
A well developed manual handling training course should include the following:
- Taking a risk management approach to your work every day
- Understanding the characteristics of hazardous manual tasks
- Learning to think and talk safety with your team openly
- Understanding the codes of practice that outline the rights and responsibilities of employers and workers
- Organisational requirements such as reporting problems of maintenance issues. -how, when and to whom?
- Understanding the risk control hieracrchy for controlling risk
- Design and engineering controls to remove the need to manual handling
Manual handling training courses can be customised with regards to course length, course contents, learning objectives and outcomes.
Our typical courses include:
- MH for the office worker/limited manual handling – 60 / 90 minutes
- MH for the worker who performs frequent manual handling – 120 – 150 minutes
What are some examples of manual handling tasks?
Manual handling is defined as:
Any activity that requires someone to exert a force in order to:
- Grasp
- Manipulate
- Strike
- Throw
- Carry
- Move (lift, lower, push, pull)
- Hold or restrain an object or body part
In the workplace this could involve:
- Handling work tools and work items
- Lifting and lowering work items and tools
- Pushing and pulling trolleys, doors
- Hold or restrain an object from moving
Questions & Free Quotes