Manual Handling Assessments To Reduce Risk, Improve Safety And Increase Profitability
Manual handling is the number one cause of injuries in the workplace, don’t wait until is too late.
We work with all industries, ranging from construction, manufacturing, transport and logistics through to councils, government departments and small businesses.
Our custom manual handling risk assessments provide a clear, logical and systematic approach to identifying hazards and managing safety in the workplace.
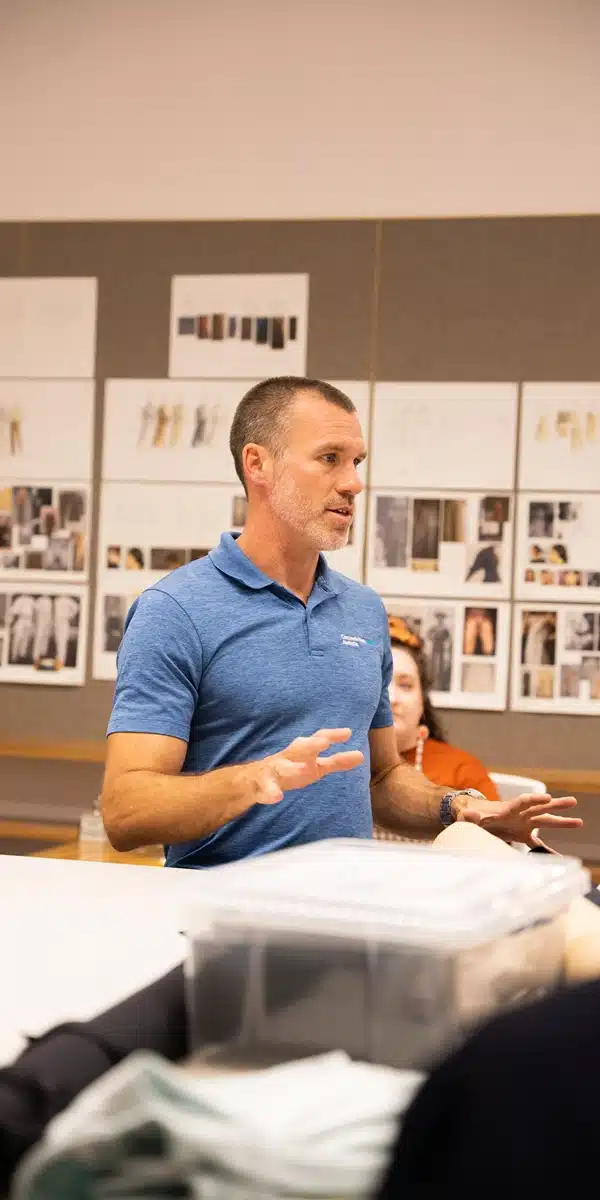
Manual Handling Risk Management Options
Risk Management Systems Assessment
Assess for gaps in your current manual handling systems
This 1.5 hour assessment is completed to assist organisations in a gap analysis of hazardous manual tasks (HMT) risk management within their organisation.
This process involves consultation with key stakeholders within the organisations, with the key objective to reduce soft tissue injuries within the organisation linked to manual handling activities.
Key elements of a thorough HMT risk management system are consulted over within your organisation to highlight any areas which may need to be improved.
Key areas reviewed are:
- Commitment policy and planning
- Consultation and communication
- Hazard identification and risk assessment
- Training and competency
What’s involved:
- Phone consultation with key stakeholders
- Site visit with key stakeholders to complete the hazardous manual task risk management assessment
- Reporting on key findings of the assessment
The outcome:
The delivery of a report highlighting key findings, strategies to improve any gaps in the organisation’s risk management systems and key expected outcomes from the integration of these strategies.
Investment:
Call 1300 519 951 to chat to our sales consultant today
Hazard Identification Assessment
Create workflow, define tasks, observe tasks & report
This service involves the following 3 steps:
- Define work flow and determine manual tasks
- Site visit & consultation with stakeholders
- Report on hazardous manual tasks including high risk tasks, body areas effected and risk factors
What’s involved:
Define work flow and determine manual tasks
- Consult stakeholders to determine work flow for phases of work and determine manual tasks that fall within the work flow
- Ensure all manual tasks are named systematically
Site visit & consultation with stakeholders
- Consult key team members on hazardous manual task risk factors
- Observe/photograph/film hazardous manual task risk factors.
Report on hazardous manual tasks including high risk tasks, body areas effected and risk factors
- Prepare a report which details name of task, body areas exposed to risk, and any hazardous manual task risk factors present
The outcome:
To provide the business with an overview of the current manual tasks within the workplace and primary manual handling hazards. This information can then be used to determine which tasks may benefit from a more detailed manual handling risk assessment and apply risk management control strategies.
Further Details:
If you would like to discuss this service for your organization please book an online meeting with one of our Directors below.
Book with Wade if you are based in QLD, NSW, ACT or NT by clicking HERE.
Book with Heath if you are based in VIC, SA or WA by clicking HERE.
Manual Task Risk Assessment
Complete a manual handling risk assessment on one workplace task
This service involves the following 3 steps:
- Identification of high risk manual task or task requiring risk assessment
- Site visit, consultation and risk assessment with key stakeholders
- Risk assessment report including assessment of tasks for hazardous task risk factors and provision of control measures according to the risk control hierarchy.
Complete Corporate Manual Tasks Solution
Define tasks, observe tasks, risk assessment / control and training solutions
This service involves the following 8/9 steps:
- Define work flow and determine manual tasks
- Site visit & consultation with stakeholders
- Report on hazardous manual tasks including high risk tasks, body areas effected and risk factors
- Complete manual task risk assessments
- Recommend control measures
- Control measure review
- Safe work procedures development
- Manual handling training options
- Pre employment / Functional capacity Testing – Injury prevention
What’s involved:
Define work flow and determine manual tasks
- Consult stakeholders to determine work flow for phases of work and determine manual tasks that fall within the work flow
- Ensure all manual tasks are named systematically
Site visit & consultation with stakeholders
- Consult key team members on hazardous manual task risk factors
- Observe/photograph/film hazardous manual task risk factors.
Report on hazardous manual tasks including high risk tasks, body areas effected and risk factors
- Prepare a report which details name of task, body areas exposed to risk, and any hazardous manual task risk factors present
Complete manual task risk assessments
- Complete manual handling risk assessment on up to 10 high risk tasks OR all tasks, using an appropriate risk assessment tool
Recommend control measures
- Through consultation and external research, suggest control measures for tasks according to the risk control hierarchy.
Control measure review
- Stakeholder meeting (OHS/WHS, team leaders) to determine if control measures are reasonably practicable
Safe work procedures development
- Develop a general over arching manual handling safe work procedure OR develop task specific manual handling procedures for tasks defined in item 2.
Manual handling training options
- Education and training options include:
- Create customised online training program that workers login and complete training as part of their induction and/or every 2 years (refresher).
- Create customised online video (15-30 minutes) of MH in the workplace. Discussing MH hazards/risks and risk management, review of best practice manual handling strategies for job tasks.
- Create customised face to face manual handling training that incorporates best practice manual handling training according NSW guidance materials. Includes theory and face to face onsite technique review.
Pre employment / Functional capacity Testing – Injury prevention
- Develop individual job role job task analysis documents which outline inherent physical requirements of the job i.e. such as postural tolerances and how long a person needs to spend and frequency in a posture, weighted tolerance.
Further Details:
If you would like to discuss this service for your organization please book an online meeting with one of our Directors below.
Book with Wade if you are based in QLD, NSW, ACT or NT by clicking HERE.
Book with Heath if you are based in VIC, SA or WA by clicking HERE.
Office Work Environment Risk Assessment
Assess all the common hazards within an office environment
This 2.5-3 hour office risk assessment is a broad assessment of the entire office that includes all work areas that ensures we identify all hazards and risks.
Key areas reviewed:
- Office layout i.e. workstation layout and placement of workstations, meeting rooms and breakout room
- Workstations, job design, workload, tasks, lighting, manual handling
- Noise i.e. review of noise to determine if noise is a potential hazard for worker comfort and productivity
- Storage, Housekeeping, Cleanliness & Cleaning Methods
- Floors and Stairs
- Computers, Copying & Other Equipment
- Hazardous Substances
- Personal Protective Equipment
What’s involved:
- Conduct an office risk assessment to identify where there may be risks in the office environment and provide you with solutions to reduce the risk in the office work environment. The duration of the office risk assessment will vary depending on each company and may take between 1 hr and half a day.
- Consultation with key stakeholders such as HR, MD or Operations manager, OHS rep and office workers is required.
The outcome:
Our consultants will provide you with a detailed report on all aspects of the office risk assessment. This will highlight areas of immediate concern and provide you with solutions to help reduce the risk in the workplace.
Investment:
Call 1300 519 951 to chat to our sales consultant today
Do You Need A Ergonomic Risk Assessment?
If your work force is primarily office based and workers are spending considerable amounts of time at the computer in the office, travelling for work (interstate) or driving, then you may require a risk assessment and training in these specific work areas. CWHA currently offers a range of risk assessments specific to these areas. Find out more about these services by clicking on the links below.
Office Workstation Risk Assessment | Vehicle Risk Assessment |
Book An Online Meeting With One Of Our Directors
Our directors have over 20 years experience! A online video call is recommended for organisations wanting manual handling risk assessments or training. Choose the state you require service delivery in via the buttons below to book a FREE online meeting or call and we will find a time that suits you.
Organisations Who Trust Our Manual Handling Assessments
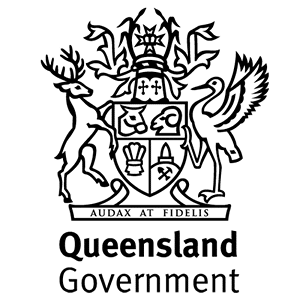
government
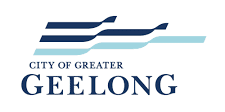
council
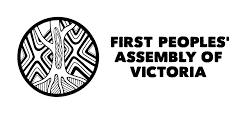
nonprofit
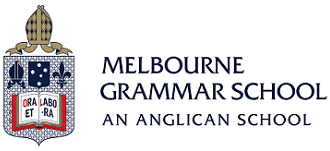
education
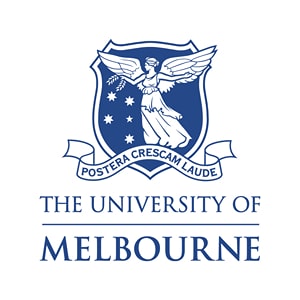
university
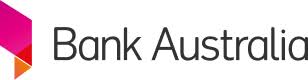
banking
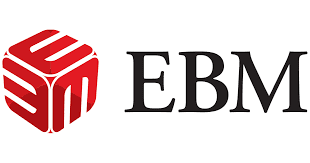
finance
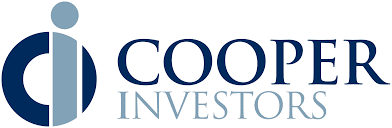
insurance

superannuation
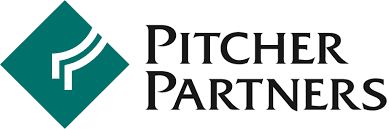
accounting
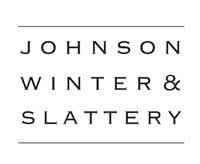
legal
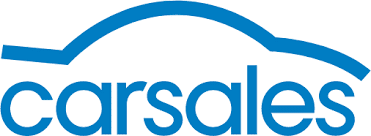
technology
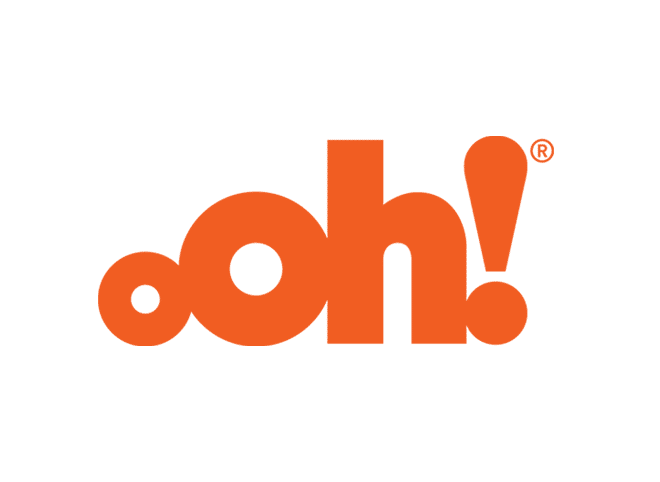
communication
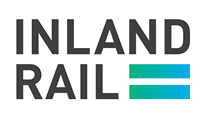
transport
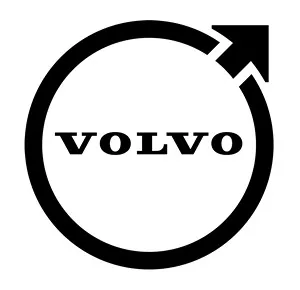
logistics
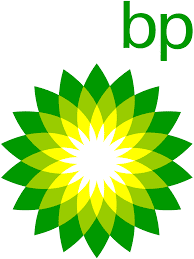
mining
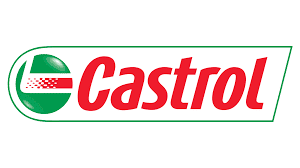
resources

manufacturing
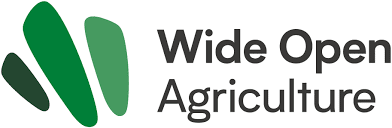
agriculture
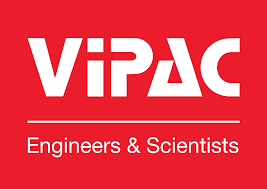
engineering
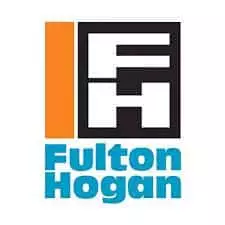
construction
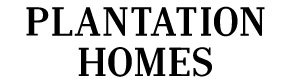
property
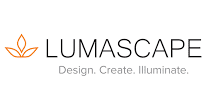
architecture
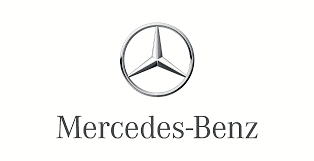
retail
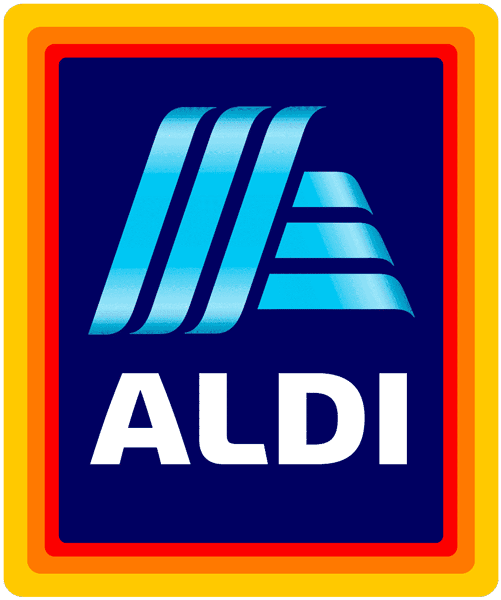
supermarket
Manual Handling Risk Assessment Case Study
A business had identified that a high risk manual handling task was being completed at one of their sites. A manager/supervisor had viewed this task and alerted his national WHS Manager. Corporate Work Health Australia was contacted to discuss how we could assist in managing this risk.
Background & Reason For Consultation
The business reached out to Corporate Work Health Australia via an online google search to discuss and be provided a quote for a face to face manual handling risk assessment and report on this one manual handling task at one of their many sites.
The task in question was completed across multiple sites with slightly different processes depending on the site and equipment available. It was determined that the task process was likely the highest risk at one site.
However, due to the travel time needed to visit this site this site was not assessed initially. It was determined internally that assessing this task at the chosen site was best as it would still allow assessment of the task which could then be commented on against other more rural sites and their processes.
Proposed Services & Implementation
Corporate Work Health Australia consulted the business to determine their assessment and reporting needs and proposed the following service –
- Background information review of task and proposed control measures to date
- Background information and review of differing processes between sites
- Onsite PErForM risk assessment of task at named site
- Consultation with worker who completes this task and supervisor at named site
- Report on current control measures and suggested control measures
Outcomes & Recommendations
Outcomes
- A face to face assessment was completed with one of our occupational health allied health professionals at the named site
- Manual handling risk assessment and report completed
- Report determined that the process at the site assessed was deemed safe and only minor improvements suggested
- Adequate control measured in place at site assessed
Further Recommendations
- Business to review report and recommendations. Report recommended further assessment and control measures for higher risk site based on description of process and consultation.
Manual Handling Assessments Are Customised To Meet Your Requirements And Exceed Your Expectations
Corporate Work Health Australia are the go-to people for those businesses leaders who realise their most valuable assets are their employees, and wish to keep them safe, healthy and productive. We tailor-design health and safety and wellness programs to the specific needs of your with our manual handling assessment.
We can assist your organisation in identifying manual handling or ergonomic hazards and potential risks, then recommend strategies to improve safety through a number of solutions that promote safe manual handling. These strategies can include, materials handling training, instructional videos, ergonomic equipment or manual task aids, safe working procedures, injury prevention, rehabilitation programs, return to work plans and more.
Read More
Manual Handling Risk Assessments Australia Wide
Have you optimised your workforce’s ability to be productive? Can you say to an absolute certainty that there are no weak areas that slow staff down in your processes, or that there is nothing they do over the course of the day that could cause them to incur an injury? If you feel your work environment is safe and that you have employed competent employees who “know what they’re doing”, but have not carried out a manual handling risk assessment to date, then now is the time.
At Corporate Work Health Australia, we believe that for the majority of companies there is a strong possibility that their processes and procedures have not been optimised and, as a consequence, that they are losing out on both productivity and potentially incurring costs as a result of worker absenteeism and injury.
The Importance of a Manual Handling Assessment
The sooner that you have a manual handling assessment completed the better. It should not be viewed as a potentially troubling report on the safety of your workspace, but instead as a proactive way to address issues that could be improved, which may, in turn, lead to knock-on benefits for the collective.
Once your practices and procedures are in line with the risk assessment and safety standards expected then fostering good practices from that point forward will help to sustain this into the future and lead to more and more efficiencies and improvements.
Once staff are educated in terms of how to best go about their work and identify manual handling hazards, the likelihood of claims for negligence and liability will also drop. As the number of workplace-related injuries and accidents fall, so too will the costs associated with these. Your productivity numbers will grow since staff will be at work more often than previously experienced and with good practices.
A workforce that sees that their employers are committed to providing a safe work environment and who recognise that efforts are continually made to improve the standards of the work that they complete will undoubtedly feel much more appreciated. This will improve the overall morale of the company, which can have a positive effect on productivity and profitability. We also run train the trainer courses so that your workplace can be up skilled in manual handling assessments when new employees come on board.
Manual Handling Safety Assessment is Good for Business
How many of your employees do you think would respond positively to the thought of incurring an injury while at work that meant their evening or weekend plans would be disrupted? Very few, we imagine. While the idea of time off work might appeal to some, the truth is that sick leave is something that very few people ever want to face. Simple mistakes and oversights in terms of work procedures can, however, lead to accidents, which is why a manual handling safety assessment is a worthwhile undertaking to identify manual handling risks no matter what industry you occupy.
A safe workplace is one that promotes a greater sense of staff morale and motivation. Employees who can see that their employers take an interest in the safety standards of their workstations and invest in ergonomic furniture to make it possible for them to do their best work appreciate the consideration. It motivates them to work harder and it gives them every opportunity to advance and reach their potential.
At Corporate Work Health Australia, our assessments are a highly effective, tailor-made means of finding the flaws in your workplace and work systems by assessing manual handling processes. By implementing changes based on our observations, a business can expect to cut its levels of absenteeism. Less sick leave or time required to engage with doctors or physiotherapists means more time to remain productive, which drives profitability.
Job Site Manual Handling Assessment
In the workplace, there are many manual handling hazards that your workers are exposed to in their daily tasks. While you may be aware of some of them, there could be hidden ways that your workers are being put at risk that have yet to be identified.
By hiring an external consultant such as Corporate Work Health Australia to complete your manual handling job site assessment, you can know that your processes have been independently checked to ensure the best working environment for your employees.
While no one wants to hear that their workplace and the processes that happen there are unsafe, by flagging up potential issues now, you can save a lot of money in the future. With a manual handling assessment, your areas of weakness can be addressed, creating a safer environment for all.
A Professional Job from the Experts at Corporate Work Health Australia
By investing now, you can protect the future of not only your employees but also your business. An expensive lawsuit as a result of negligence at work can be devastating. The good news is that by identifying the manual handling hazards and risks, putting methods and training in place to avoid injuries and accidents, you can minimise the risks.
Contact Corporate Work Health Australia today for your manual handling risk assessment and feel confident that you have been equipped with the knowledge that gives you the power to protect your most valuable asset – your staff.
Process
1. Enquiry
Call, email or complete a form. Let us know what you want to achieve or the problems you are having.
2. Consultation
Phone, video call or face to face. We will discuss your needs, make some suggestions and provide a quote.
3. Assessment
Your assessment and/or training package is 100% tailor made to suit your needs, budget and service requirements.
4. Training
Onsite, online or both. Your personalised package is delivered by health professionals with extensive clinical and teaching experience.
5. Results
We have helped thousands of people at some of Australia’s top companies. Our team will work with you every step of the way to ensure you achieve the right results for your company and for your workers.
Manual Handling Assessment Benefits For Companies
Corporate Work Health Australia can assist your organisation in identifying manual handling and ergonomic risks and develop strategies to reduce manual handling hazards and increase safety.
Benefits to your business:
- Financial savings
- Healthier employees
- Increased productivity
- Improved morale
- Fewer injuries
- Quicker recoveries
Manual Handling Assessment Benefits For Employees
Manual handling risk assessment requires a collaborative approach that will engage workers to proactively identify hazards. It empowers them to be solution orientated and ultimately be in charge of their own safety.
Benefits to you team:
- Increased consultation and collaboration in the workplace
- Empowering workers to be solution focused
- Healthier and happier workers
- Increased productivity
- Fewer injuries due to safe manual handling
Free Basic Manual Handling Risk Evaluation
Answer a few questions and receive a free online consultation with one of our highly experienced occupational health professionals
Frequently Asked Questions
What constitutes a Manual Handling operation?
Manual handling is defined as:
Any activity that requires someone to exert a force in order to:
- Grasp
- Manipulate
- Strike
- Throw
- Carry
- Move (lift, lower, push, pull)
- Hold or restrain an object or body part
Workers who perform these tasks are at risk of manual handling injuries. Workers should be educated on manual handling risk management and best practices relating to manual handling. Contact us at Corporate Work Health Australia
What are my responsibilities as an employer under the law?
When it comes to health and safety, the PCBU (person, company or business undertaking), also known as the employer, has a duty of care to provide a safe workplace, ensure they have appropriate risk management strategies in place and provide the appropriate PPE and training to employees/workers.
Workplaces where workers undertake manual handling as part of their job role should be undertaking manual tasks hazard identification, manual handling risk assessments and provide risk management and manual handling training as part of their overall OHS risk management process.
Workers who undertake manual handling on a daily basis are likely to benefit from manual handling training on a regular basis (6 monthly or annual basis), whereas workers who infrequently handle loads i.e. office workers may only need training every 2 years as their risk exposure is less.
What is a Risk Assessment?
A manual handling risk assessment focuses on identifying manual handling hazards and then assessing the risks in consultation with the worker(s).
The risk assessment will look to identify which body regions are impacted and will look to score the risk in proportion to what’s observed.
When undertaking a risk assessment, we will observe and look to manage the following:
- repetitive or sustained force
- high or sudden force
- repetitive movement
- sustained or awkward posture
- exposure to vibration
The focus of the risk assessment should be focused on the risk control hierarchy that looks to:
Level 1. Eliminate manual handling
Level 2. Substitute the hazard with something safer. Isolate the hazard. Reduce the risk through engineering controls
Level 3. Administrative controls i.e. job rotation, rest breaks, manual handling training
There are many types of manual handling risk assessment that can be used. Common examples include the PerFORM risk assessment, MaNTRA risk assessment, REBA risk assessment.
How do I assess Risks in my workplace?
Assessing risks in the workplace involves several steps that include:
- Review of current injuries in the workplace i.e. body region, reason for injury, review of incident report
- Review of hazard report and near miss reports
- Consultation with stakeholders i.e. workers regarding current perceived/identified hazards/risks and body regions impacted
- Selection of risk assessment tool
- Performing of risk assessment
What are the recommended weight limits for lifting?
Neither the regulations or codes of practice specify weight limits for lifting.
This is because there are many factors that impact on the risk, not just the weight of the item being handled.
Some workplaces will implement weight limits for single or dual person lifting as well as weight limits according to height ranges. They have likely implemented these internal company policies and procedures as part of their manual tasks risk management process.
Do employees have responsibilities?
When it comes to manual handling in the workplace, employees have the following responsibilities:
- Follow all reasonable instructions in relation to manual handling procedures
- Engage in the consultative process
- Report manual handling hazards to their immediate supervisor/branch manager; and
- Undertake and apply manual handling training as required
Can I implement a “No Lifting Policy”?
A workplace can implement their own policies and procedures with regards to manual handling, however it is important that the business/employer understands the practicality of doing so. In many workplaces it is simply not feasible or practical to implement a no lifting policy as there is likely to be some type of manual task to be conducted in a workplace. Therefore creating a policy that workers/employees cannot adhere to is not appropriate.
In many circumstances a business may look to implement a no lifting policy with regards to a specific task or item. Mechanical aids may be more appropriate to move the load and the hazard/risk associated with manually moving these loads may be too great. A business is likely to ensure they have a safe work method statement relating to how this task should be performed.
What are some examples of manual handling tasks?
Manual handling is defined as:
Any activity that requires someone to exert a force in order to:
- Grasp
- Manipulate
- Strike
- Throw
- Carry
- Move (lift, lower, push, pull)
- Hold or restrain an object or body part
In the workplace this could involve:
- Handling work tools and work items
- Lifting and lowering work items and tools
- Pushing and pulling trolleys, doors
- Hold or restrain an object from moving
Questions & Free Quotes